|
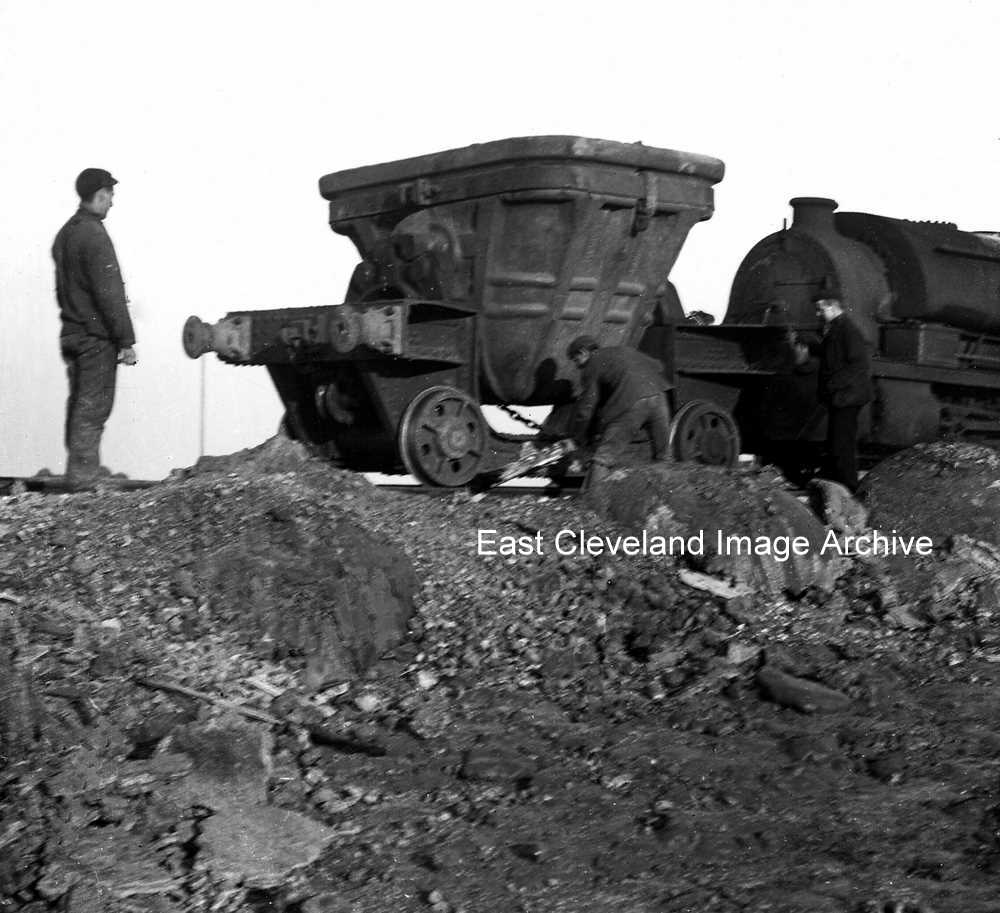
Well…not quite. The tip labourer is spragging the wheel of the slag Bogie prior to tipping the slag over Cattersty Cliffs.They were tipped by using a chain and winch system through the hook on the side of the pots (on the other side of ladle). You can just see the chain hanging below the pot, to the left of the labourer. The Loco is one of the Low height types used on the Blast Furnaces. It certainly cast a lovely glow over the scene at night!
Image courtesy of Dave McGill (a glass plate negative).
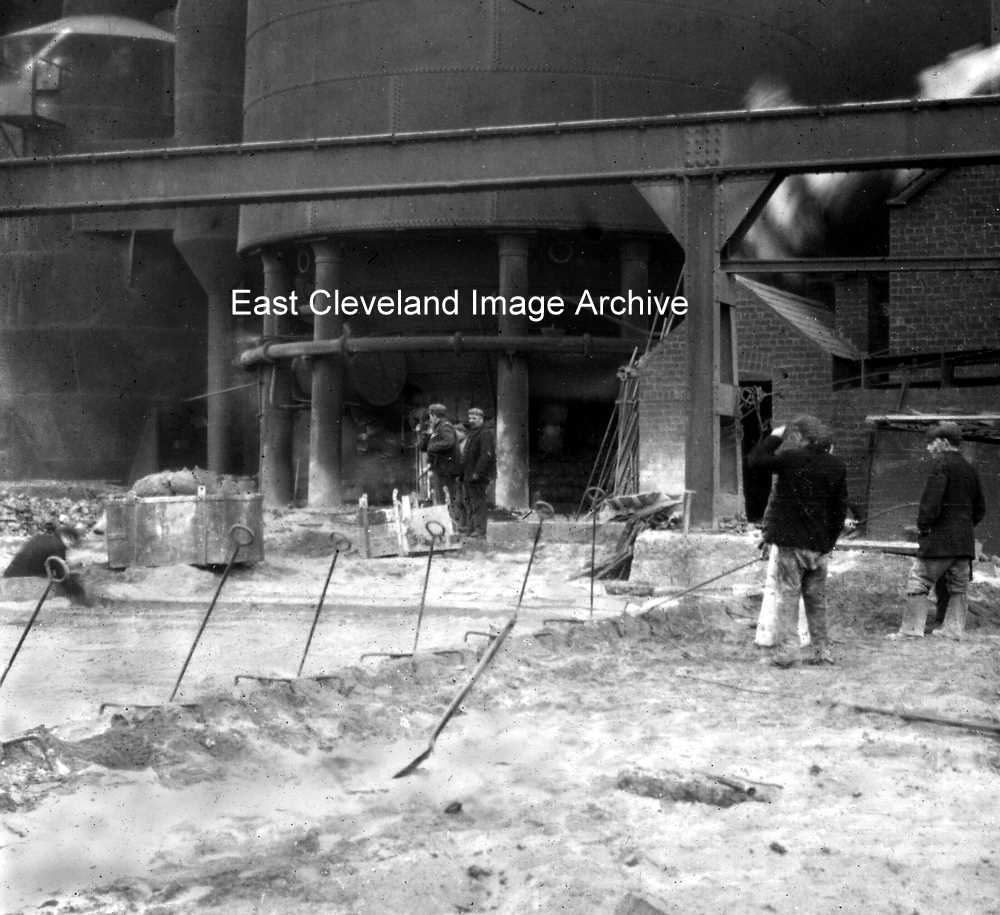
A pig bed with the gate irons in place ready to divert the flow of metal to fill the pigs.
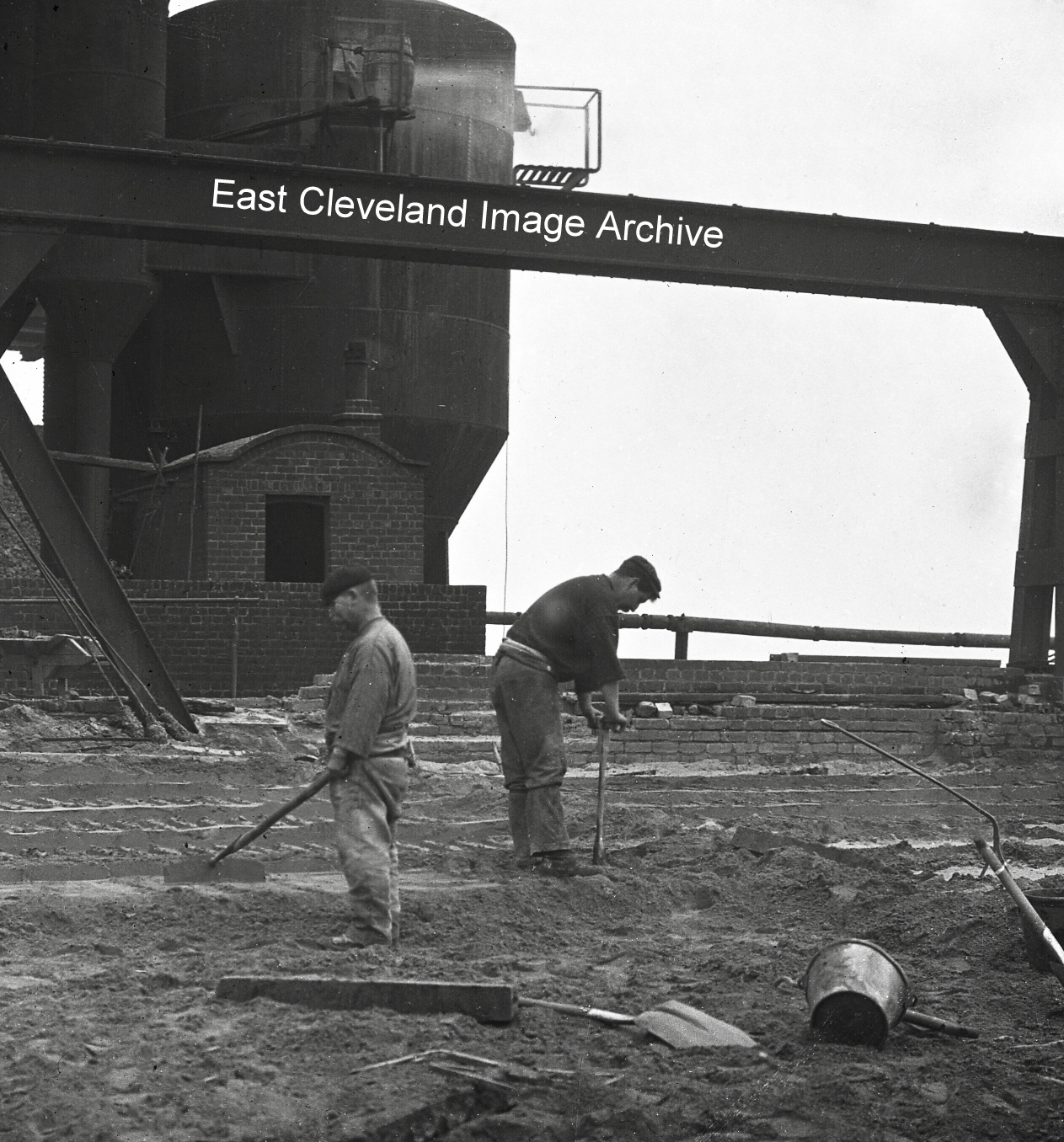
These two men are preparing the sand runners (sows) and moulds (pigs) to receive the molten metal from the blast furnace.
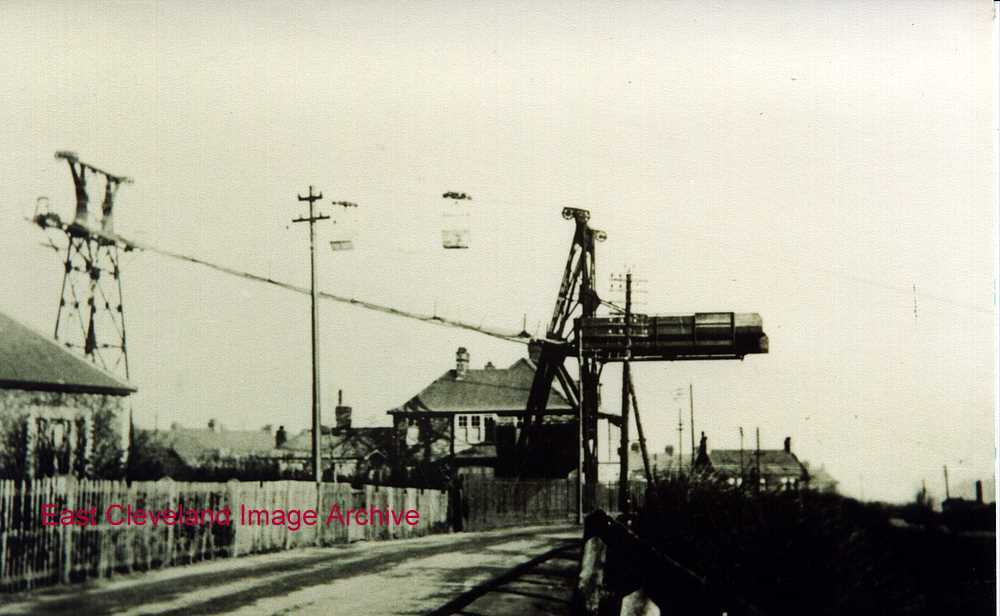
The aerial ropeway which transported ironstone from North Loftus (Skinningrove) mine. Rodney Begg remembers: “This section (without its protective screen over the road) was still in place when I started at Skinningrove – although the roadside pylon disappeared soon after – but the left-most pylon survived to become a lighting tower!”.
Thanks to Rodney Begg for that memory.
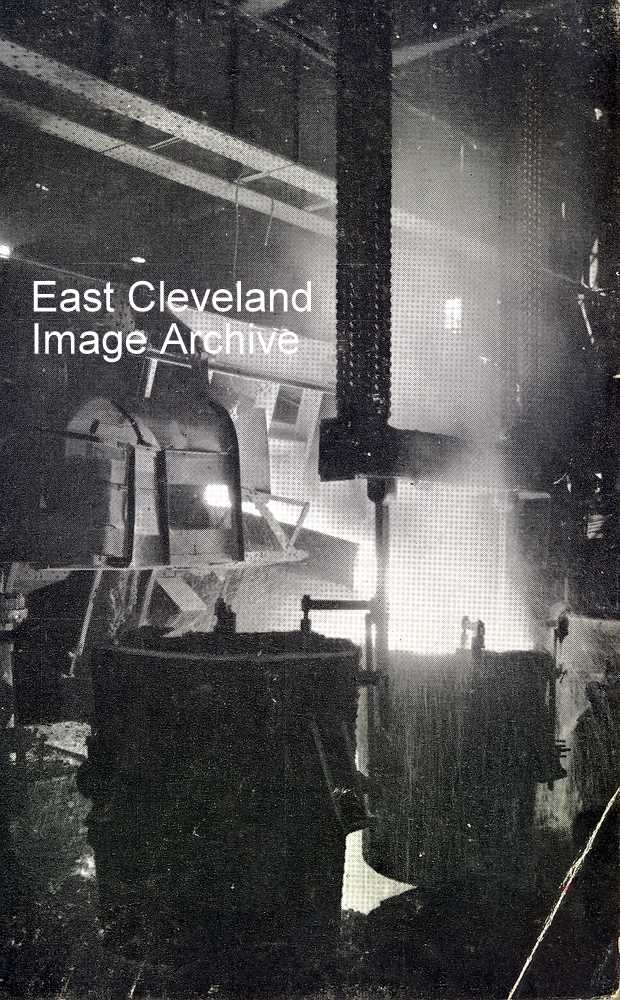
This image of A furnace first tap with number 1 (75 ton crane), before the main hoist chains were changed to wire ropes. After the 8 (or 12 for the ’Big’ furnaces) hour process of turning a charge of cold and hot metals into steel, the climax usually came quickly after a flurry of samples of steel and slag to the shift lab. The hooter would sound, the bangalore torpedo (more precisely ’the shaped charge’) would blow out the tap hole and the furnace would heel over to discharge it’s first potful of molten metal. Eric Johnson told us: “The scene always reminded me of what I thought Dante’s Inferno would look like – flames up to the rafters, (sometimes bringing a flurry of pigeons down), the furnace hand on the tapping stage hurling the alloying charges of coal, niobium, ferro-manganese etc. surrounded by smoke and light and heat. The furnace tilting further and further with each potful until it was spent. The pots in their turn travelling sedately to the Ingot Shed across the way and charging rake after rake of ingot moulds with the liquid metal. Sometimes a ’flying stopper’ made it more hazardous to empty the pots as it was then impossible to stop the flow of metal between moulds and everybody in the Ingot Shed would get a scorching (if they were unlucky they’d get a lot worse!) – and, as Bob says, a wet pot could create a shower of incandescent metal dancing around the pitside”. Stan Henderson tells us: ”Awesome! Better than any fireworks display I have seen.”
Thanks Eric Johnson and Stan Henderson for the updates.
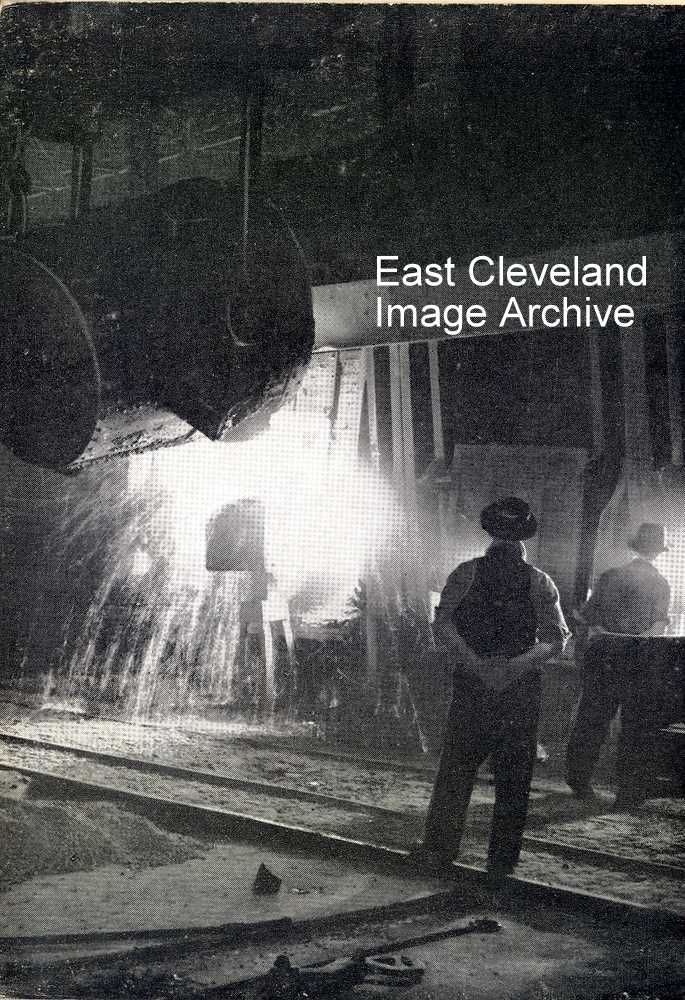
This was always a beautiful sight to behold – a portable spout was placed into the gaping door (usually an end one) of the furnace and with its siren whooping the crane would manouevre the sizzling pot of iron over it, then delicately empty the pot into the furnace – bringing memories of bonfire night! Eric Johnson told us: “The chap in the foreground with his back towards the camera is Sid Carter, also note the sample pot”. Rodney Begg has advised: “I think this must have been taken on my shift (’C’ shift I think it was ), because I recognise the first hand with his back to the camera, he used to let me fettle for him as ’acting-temporary-fifth hand’! We were kept us busy around tapping time (taking a sample) and the sample lad ( a Theaker from Boosbeck, I think) used to curse if the sample was over-quenched and wouldn’t drill! Sid was always impatient – he would wait in the balance room/bait room pacing up an down while Stan (or Derek, the 2nd Chemist) did the analysis – as a lowly 3rd Chemist I was only allowed to do slags and iron samples!”.
Thanks to Eric Johnson and Rodney Begg for the updates.
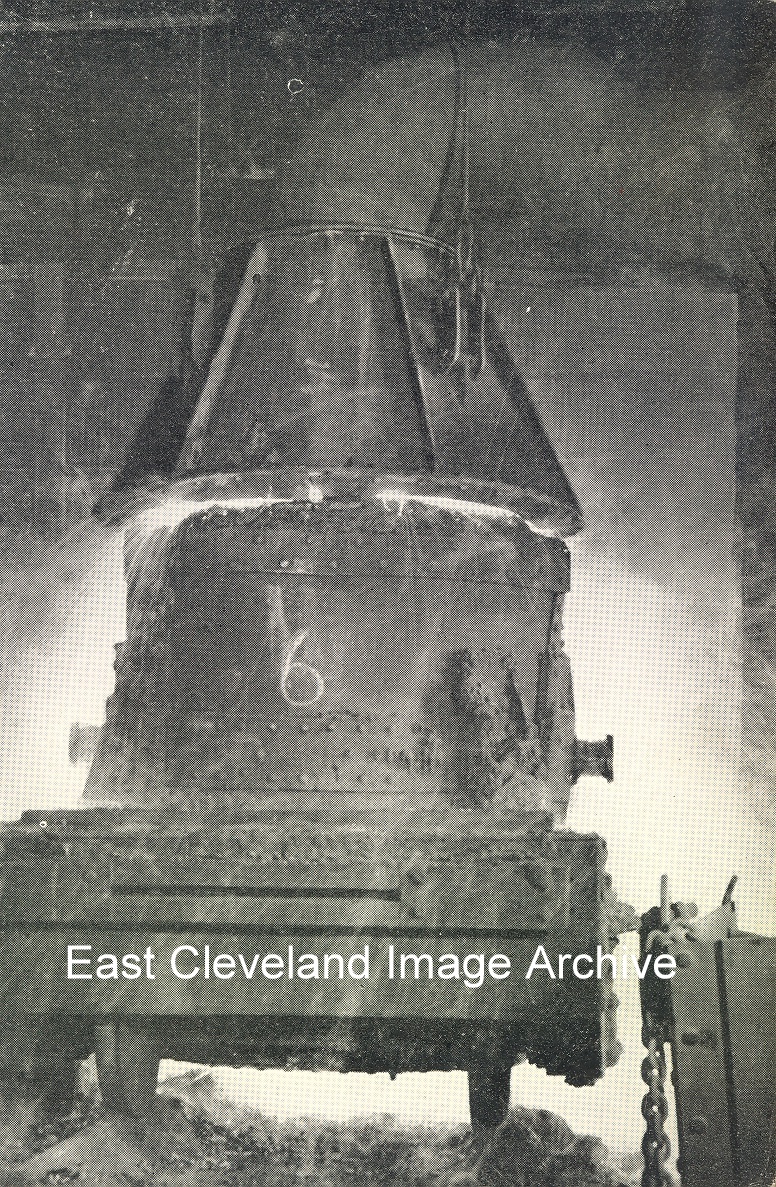
Rodney Begg tells us of de-siliconizing: “When I was at Skinningrove this had fallen out of favour and the equipment lay at the end of the Talbot’s, next to ’D’ furnace. Sound in principle and obviously successful in other areas (this is the basis for Basic Oxygen Steelmaking), it never seemed to catch on at Skinningrove!”.
Thanks to Rodney Begg for this observation.
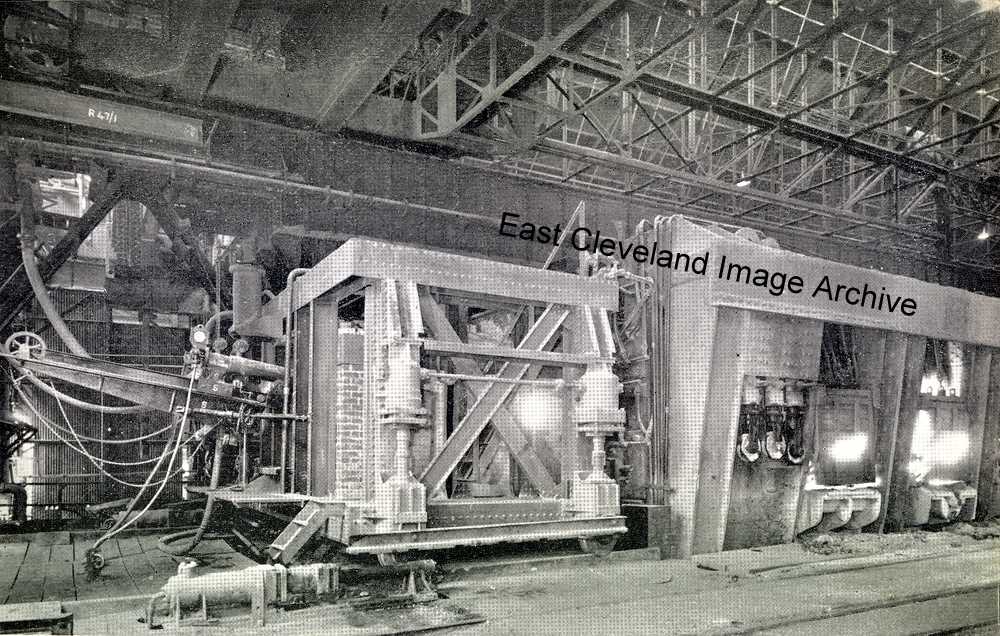
Of the 300 ton steel furnace; Rodney Begg told us: “This is the view I used to get just out of the door of the Shift Laboratory on the Talbot’s; the ’A’ end of a furnace (in this case either ’B’ or ’C’). It is easy to see the difference between this image and the image of the gas-fired one in an earlier post. The burner end is mobile for maintenance and carries much more complex pipe work”.
Thanks to Rodney Begg for the update.
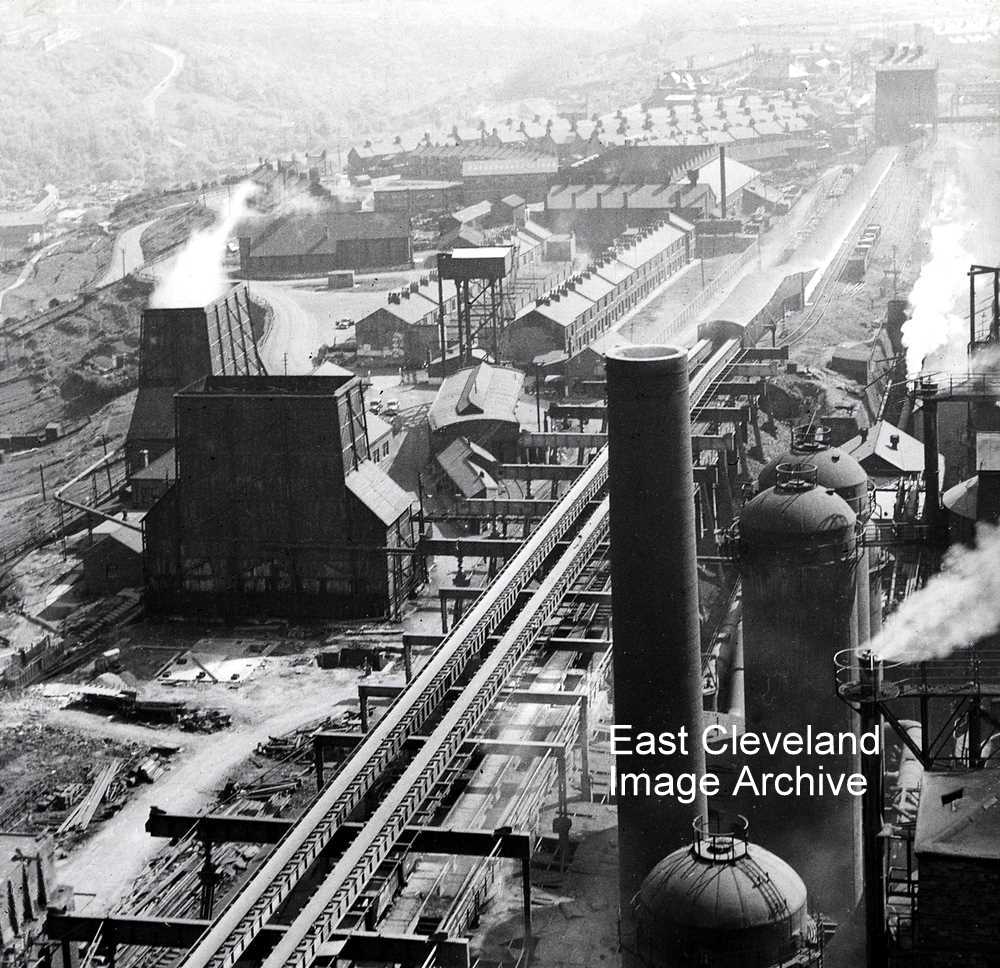
Taken from the top of No. 5 perhaps (maybe during its construction in the 1950’s?). A different view of the iron and steel works, looking inland, and down into the valley; the two rows of Furnace Cottages can be seen. Rodney Begg told us: ”I spent the last 12 years or so of my employment here as a metallurgist in the bottom Test House (just to the right of the water tower and partly hidden by the tall chimney, nearly in the centre of the picture)”.
Thanks to Rodney Begg for the update.
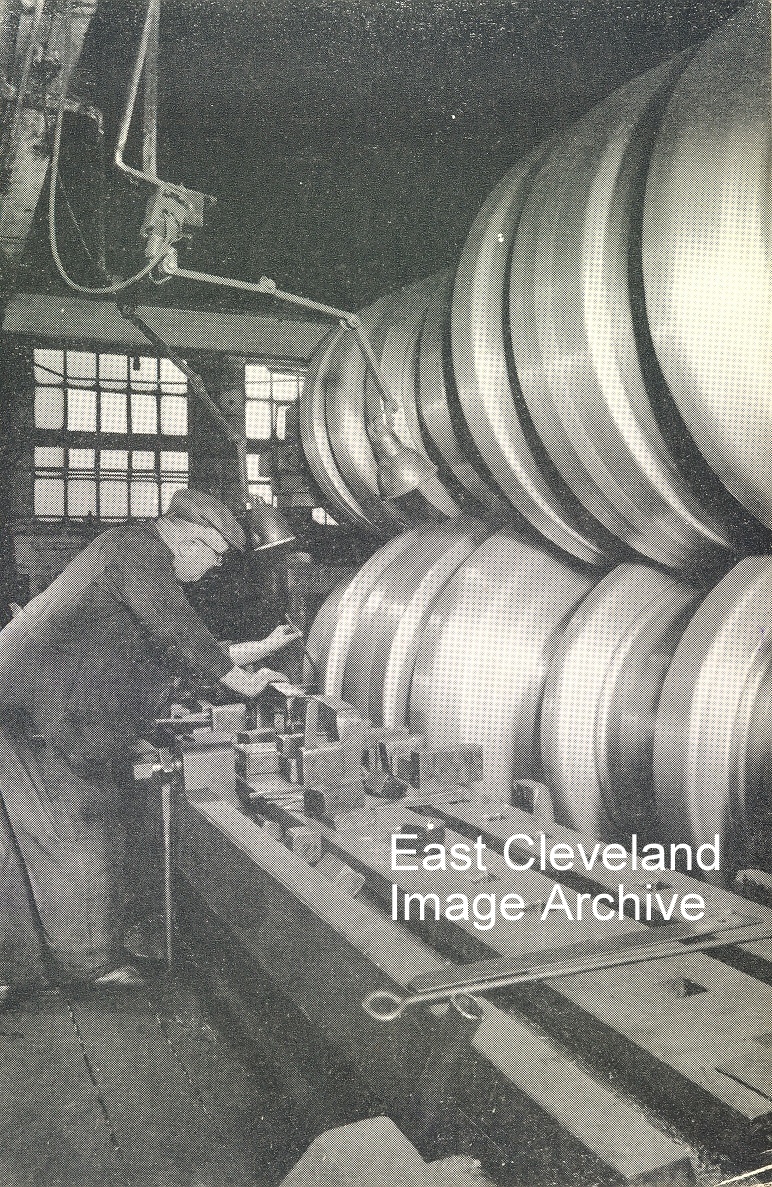
Skinningrove Rolling Mills evolved as completely self-sufficient units, capable of developing the rolls for new sections and manufacturing them from blanks. A number of highly skilled men were involved; from the draughtsmen drawing up the profiles, the pattern makers manufacturing the cut profiles for the roll turners to manufacture. Mike Hore told us: “The roll turner in the photograph is Harry Roberts. I worked with him on the same shift for a number of years before I left the Steel Industry. In addition the photograph was taken in the old roll shop which was situated under the mill arch and under the mill gantry crane. The picture was probably taken in the late 1960’s since the present roll shop came into operation in roughly 1971/72”. Ken Johnson also told us: “I trained as a teacher with Mike Hore. Mike was able to write “Skinningrove” in mirror writing as quickly and efficiently as writing in normal writing.. I wonder if Mike could still do that?”.
Thanks to Mike Hore and Ken Johnson for the updates.
|
|
Recent Comments